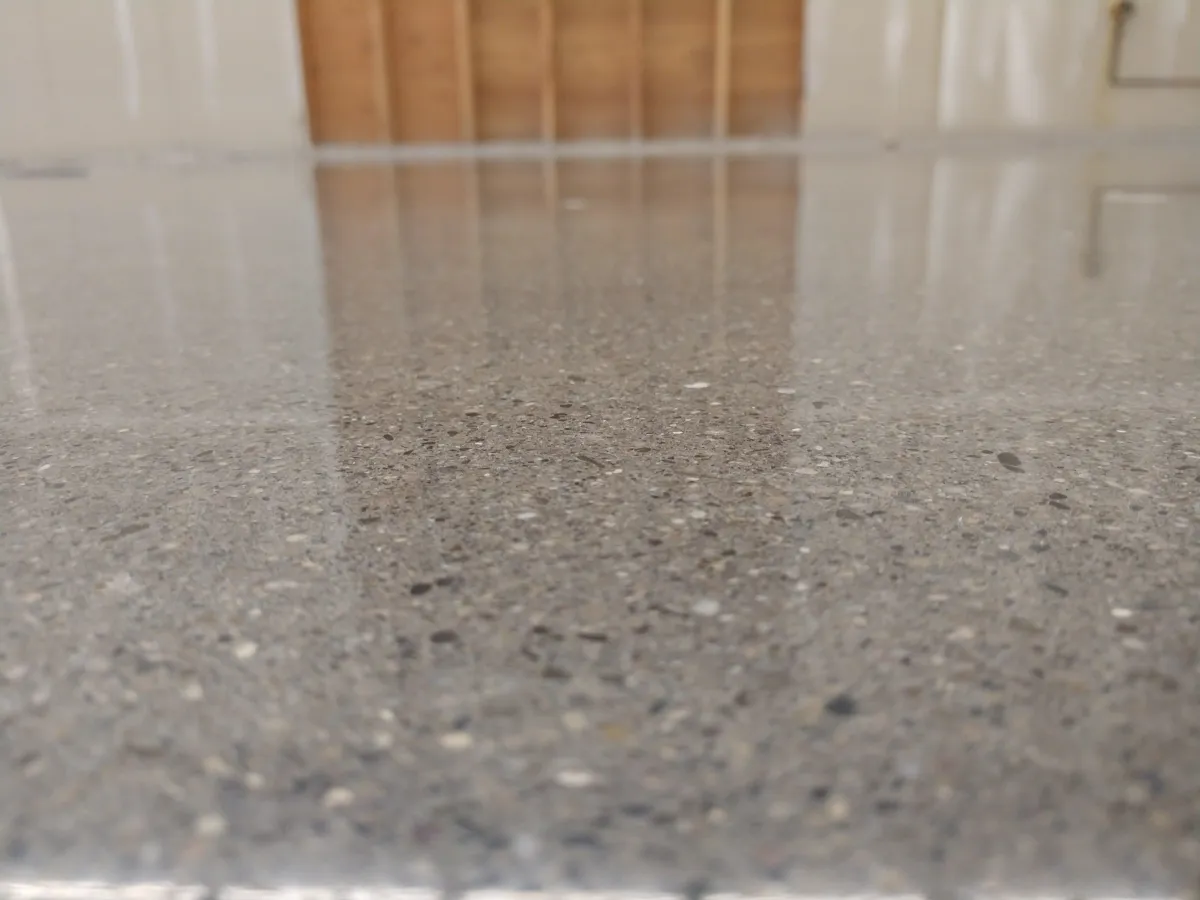
Concrete Coating vs. New Concrete Floors: The Smart Upgrade for Twin Falls Homeowners
Concrete Isn’t Forever—But You Don’t Always Need to Replace It
Concrete is tough, no doubt. But even the best slabs around Twin Falls take a beating over time—especially in garages, basements, patios, and driveways where they’re exposed to everything from hot tires to winter salt to years of wear and tear. Eventually, they all start showing their age.
And that’s when most homeowners start asking the big question: “Should I rip this out and pour a new floor?”
Here’s the thing—ripping out concrete isn’t cheap. It’s messy. It takes time. And in many cases, it’s just not necessary.
That’s where coating and resurfacing come in. Whether it’s a garage floor that’s stained and pitted, or a patio that’s cracked and tired-looking, resurfacing or applying a high-performance epoxy system can give your existing concrete a second life—without the cost and headache of starting from scratch.
At ORR Floor Care, we’ve helped hundreds of homeowners throughout Twin Falls, Jerome, Burley, and surrounding Idaho communities avoid unnecessary replacement by transforming their existing concrete with proven coating and resurfacing systems.
In this guide, we’ll break down the real difference between coating, resurfacing, and full replacement—and help you figure out which route actually makes sense for your home. We’ll cover what concrete coatings are, when resurfacing works, when replacement is truly necessary, and what you can expect in terms of cost, timeline, and long-term results.
What Happens to Concrete Over Time?
Concrete might be one of the most durable materials used in home construction, but it’s far from invincible—especially in Southern Idaho. Around Twin Falls, we deal with a unique mix of environmental stressors that can really wear on a slab. From freeze-thaw cycles in winter to dry summer heat and everything in between, the concrete around your home goes through a lot.
Here’s what we typically see:
Surface Cracking
Hairline cracks, spiderweb patterns, or deeper joints that widen over time—it’s all part of how concrete reacts to temperature changes, ground movement, and settling. Most of the time, these cracks are cosmetic. But if water starts to seep in and freeze, they can spread and worsen fast.
Spalling and Chipping
That flaky, dusty layer peeling off the surface? That’s called spalling. It usually happens when moisture, salt, or poor finishing practices during the original pour cause the surface to degrade. We see this a lot in older garages and outdoor slabs that haven’t been sealed or maintained.
Staining and Discoloration
Bare concrete absorbs just about anything that touches it. Oil, grease, rust, fertilizer, paint—you name it. Over the years, stains become more permanent, and power washing can only do so much. You’re left with a surface that always looks dirty, even if it’s structurally fine underneath.
Efflorescence
That white, chalky stuff coming out of your concrete? It’s called efflorescence—basically salt deposits brought to the surface by moisture vapor. While it’s not harmful, it’s a clear sign your concrete is breathing out moisture, and it’s a red flag if you’re planning to coat or seal without proper prep.
Dusting and Wear
In garages and basements, you might notice a fine powder on the surface. That’s called dusting. It happens when the top layer of concrete wears down or wasn’t finished correctly. It’s messy and makes it hard to keep the space clean.
So the question is—does all this mean you need to replace the slab? Not necessarily.
If the slab isn’t heaving, sinking, or showing signs of serious foundational damage, you’ve got options. Most of the issues listed above can be repaired, coated, or resurfaced with the right system. The key is understanding what condition your concrete is really in—and choosing a solution that adds value instead of wasting money on unnecessary demo work.
That’s what we’re going to dig into next: what full replacement actually involves—and why it’s often the last resort, not the first.
The Smart Alternative: Coating or Resurfacing Your Concrete
Here’s the truth most contractors won’t tell you: you don’t need to replace your concrete just because it looks bad.
In fact, as long as your slab is structurally sound—meaning it’s not sinking, buckling, or falling apart beneath your feet—you’re likely a great candidate for resurfacing or coating. And if you live in Twin Falls or anywhere in the surrounding area, this option makes a lot more sense for your wallet, your schedule, and your long-term peace of mind.
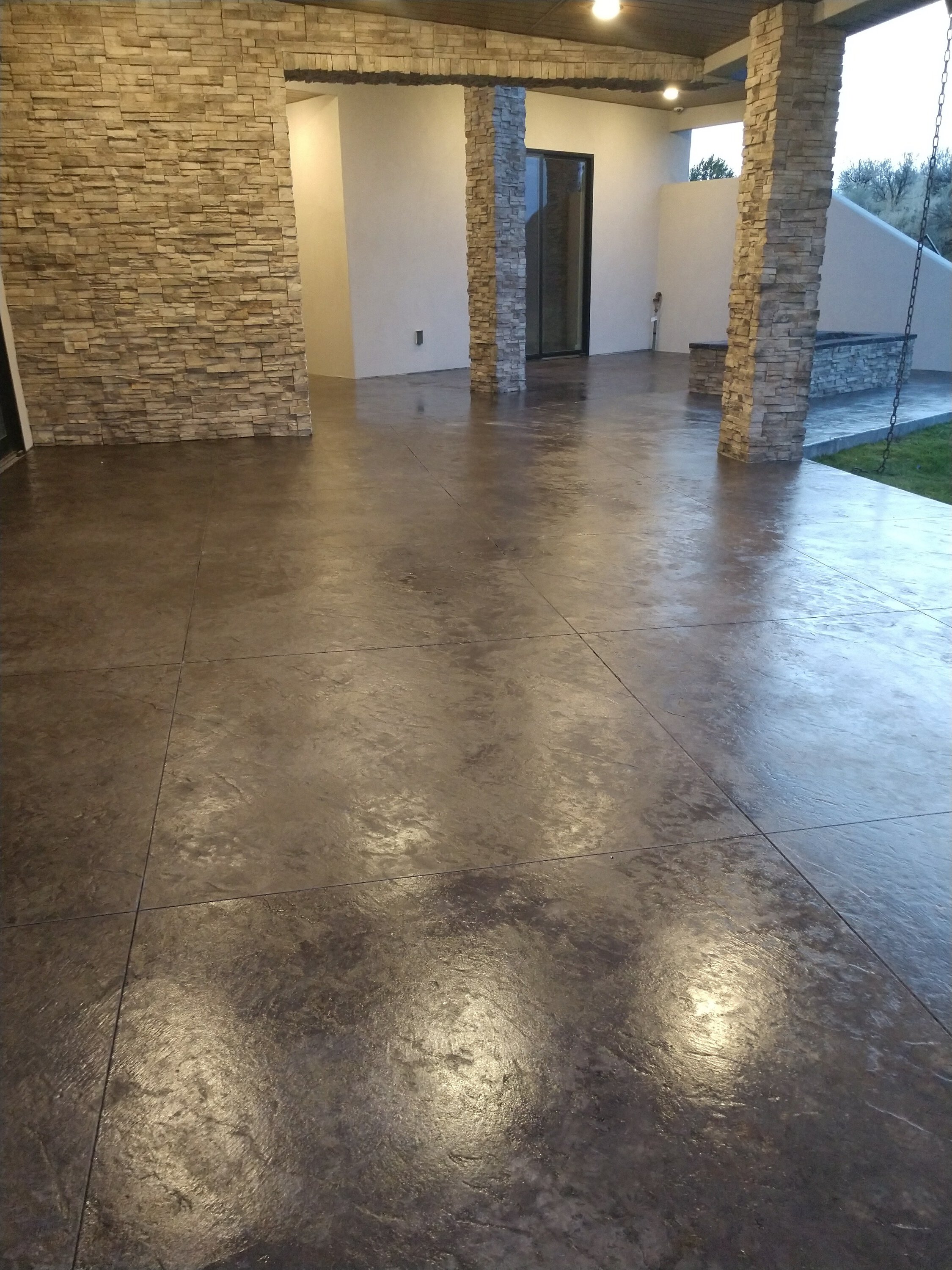
Let’s Break Down the Options
First, some quick definitions:
Concrete Coating – This refers to a surface system applied on top of your existing concrete. Think epoxy, polyaspartic, or urethane. These are durable, customizable finishes that bond directly to the slab.
Concrete Resurfacing – This means applying a new thin layer of polymer-modified cement (called a microtopping or overlay) over the old slab. It covers imperfections and creates a clean, like-new surface ready for staining, polishing, or sealing.
Both options can completely transform your floor—but the best choice depends on how your current concrete looks and what kind of finish you're after.
Where These Options Shine
At Orr Floor Care, we’ve used coatings and resurfacing systems all over Twin Falls in places like:
Garage floors that are stained, cracked, or dusty
Basements with uneven or unattractive finishes
Outdoor patios and walkways that need a facelift
Entryways where curb appeal matters
Laundry rooms, shops, and utility spaces that need durability with easy cleanup
If the goal is to refresh the look and improve functionality without tearing everything out, coating or resurfacing is the way to go.
Less Time, Less Mess, Lower Cost
Compared to full replacement, resurfacing or coating your concrete comes with three big advantages:
It’s faster. Most coating jobs take 1–3 days. No weeks-long curing time, no torn-up yard, no hassle.
It’s cleaner. No jackhammers or dump trucks—just grinders, repair materials, and skilled hands.
It costs less. Most coating or resurfacing systems fall in the $4–$8 per square foot range, depending on condition, prep, and finish. That’s nearly half the cost of replacement.
And the result? A floor that performs better, looks cleaner, and resists wear, moisture, and stains far better than bare concrete ever could.
Aesthetic Upgrade Without Structural Work
Want a high-gloss, flake epoxy garage floor that turns heads? We can do that. Need a decorative patio overlay that looks like natural stone? No problem. Want polished concrete in your basement that’s sleek, durable, and easy to clean? Absolutely.
These systems don’t just hide imperfections—they enhance your entire space. With dozens of finishes, colors, and textures available, coating and resurfacing turn plain gray slabs into design features.
Before you commit to tearing out a floor that still has life in it, talk to someone who actually knows how to bring concrete back from the brink. In the next section, we’ll dive deeper into epoxy and other coating systems, and what homeowners should know before choosing one.
Epoxy and Coating Systems: What Homeowners Should Know
You’ve probably heard of epoxy floors, especially if you’ve ever looked into upgrading a garage or basement. But not all epoxy is created equal—and there’s a big difference between what you buy at a home improvement store and what a professional like Orr Floor Care installs.
Let’s clear the air and talk real coatings—not cheap paint kits, but durable, industrial-grade systems that actually perform.
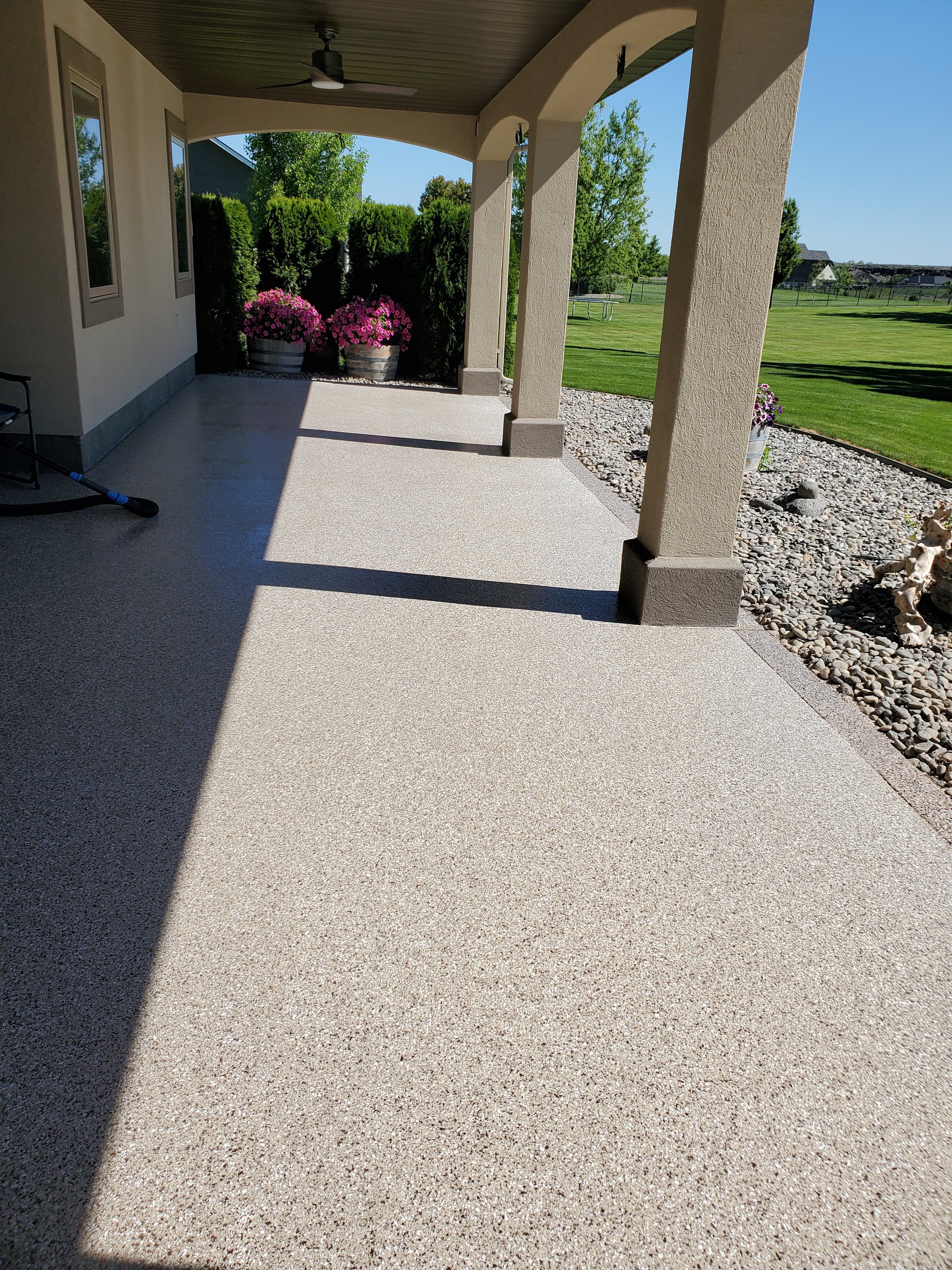
What Is Epoxy—Really?
Epoxy is a two-part thermoset resin. When Part A (resin) and Part B (hardener) are mixed, they create a chemical reaction that bonds to concrete and cures into a hard, plastic-like surface. Unlike floor paint, which just sits on top, true epoxy soaks into the surface and becomes part of the slab—if the prep is done right.
The result? A floor that resists:
Oil and chemical stains
Hot tire pickup
Scratches and abrasion
Moisture intrusion
UV damage (when combined with a polyaspartic or urethane topcoat)
It’s not just durable—it’s customizable too. You’ve probably seen flake epoxy with that granite-chip look, or metallic epoxy with swirling color blends that mimic marble or stone. These finishes aren’t just eye-catching—they’re practical and long-lasting.
System Options for Twin Falls Homes
Orr Floor Care installs multiple coating systems, each suited to different spaces and needs:
Solid Color Epoxy – A clean, professional look, ideal for garages, shops, and utility rooms
Flake Systems – Decorative, slip-resistant, and excellent for hiding imperfections
Quartz Broadcast Systems – Tougher than nails; great for high-traffic areas needing extra grip
Metallic Epoxy – A statement finish for basements, showrooms, or modern interiors
Polyaspartic Topcoats – Fast-curing, UV-stable, and highly resistant to abrasion and chemicals
What you choose depends on how you use the space. Garages with frequent car traffic? Go flake or quartz with a polyaspartic topcoat. Want something modern for the basement? Metallic epoxy might be your best friend.
Prep Work Is Everything
One thing to understand—it’s not the coating alone that makes the floor last. It’s the prep.
We see a lot of DIY kits peel or fail because the surface wasn’t ground, cleaned, or moisture-tested properly. At Orr Floor Care, every coating job starts with mechanical diamond grinding, joint and crack repair, and full surface evaluation. It’s not flashy work, but it’s what makes a coating stick and stay stuck.
When done right, a professional-grade epoxy floor can last 15–20 years or more, even under heavy use.
So, if your garage floor is still structurally sound but looks like a warzone, coating it with a system that’s made to last isn’t just a smart move—it’s one that pays off.
Next, we’ll talk about how to tell if resurfacing makes more sense than replacement—and how to spot when it’s time to call it quits on a slab.
When Resurfacing Makes More Sense Than Replacing
Most concrete slabs in Twin Falls don’t need to be replaced—they just need a second chance.
Unless your floor is sinking, heaving, or literally falling apart under your feet, you’re probably working with a slab that’s still structurally sound. And if that’s the case, coating or resurfacing it is almost always the smarter, more cost-effective way to go.
Let’s walk through some common concrete conditions and how we typically handle them at Orr Floor Care.
Situation #1: Cracked but Stable
A few surface cracks? Totally normal. Concrete is a rigid material—it’s going to move and settle over time. As long as the cracks aren’t wide, deep, or caused by movement in the subgrade, we can usually:
Clean them out
Fill them with flexible joint filler or patch material
Grind them flush
Coat over them with epoxy or a resurfacing layer
Verdict: No need to tear out the slab. A good prep job + professional coating = like-new finish.
Situation #2: Stained, Ugly, and Worn Out
Maybe the slab is covered in old oil stains, rust spots, or years of discoloration. It might even be dusty and chalky to the touch (aka dusting). This is where coatings shine. After grinding off the damaged top layer and cleaning the surface, a solid coating system can make the floor look brand new—and protect it for decades to come.
Verdict: If the slab’s sound, coating is the clear winner.
Situation #3: Surface Pitting and Spalling
Pitted concrete, salt damage, or flaking around the surface? It happens all the time, especially on garage floors that weren’t sealed properly or took years of abuse. If the damage is limited to the surface, we can resurface it with a microtopping or patch system and then coat it for protection.
Verdict: Don’t replace—restore and protect it properly this time.
When Replacement Is the Right Move
Now, there are times when a coating just won’t cut it:
Heaving or uneven slabs due to soil movement or frost heave
Large cracks with differential movement (where one side is higher than the other)
Sinking or voids underneath the concrete
Major drainage issues or foundational instability
In those rare cases, starting over is the safest bet—and we’ll be the first to tell you that. But again, these are the exception, not the norm.
Our approach at Orr Floor Care is simple: we don’t push coatings if they’re not the right fit. We evaluate your slab honestly and give you options that actually make sense.
In the next section, we’ll break down what Twin Falls homeowners can expect to spend—whether you’re coating, resurfacing, or replacing your concrete floor.
Budget Breakdown: What You’ll Pay (and Save) in Twin Falls
Cost is always one of the first questions we get—“What’s it going to cost me to fix this floor?” And honestly, it’s a fair question. Because whether you're resurfacing, coating, or tearing it all out and starting over, it’s an investment.
Here’s a clear breakdown of what you’re looking at in today’s market around Twin Falls and nearby areas like Jerome, Burley, Kimberly, and Filer.
Full Concrete Replacement: $8–$12 per Square Foot
Let’s say you’re tearing out and re-pouring a 400-square-foot two-car garage. You’re looking at $3,200 to $4,800 minimum—and that’s just for the concrete.
That doesn’t include:
Demolition and haul-away
Permits (if needed)
Curing time (28 days for full strength)
Any decorative finish or sealer afterward
And let’s be real—most people don’t want plain gray concrete. If you plan to coat it after the pour, you’re stacking more cost on top.
Epoxy or Polyaspartic Coating: $4–$7 per Square Foot (Installed Right)
Now compare that to coating your existing slab. For that same 400 sq. ft. space, you’re looking at $1,600 to $2,800 for a professional-grade system.
That typically includes:
Diamond grinding for surface prep
Crack and joint repair
Moisture testing (if needed)
Base coat, flakes (optional), and a durable topcoat
10–15+ year performance with proper care
And you’re not waiting a month to use your garage. You’re usually walking on it in 24 hours and parking on it in 48–72.
Concrete Resurfacing or Microtopping: $5–$8 per Square Foot
If your concrete surface needs more cosmetic help—think deep pitting, spalling, or ugly texture—you might need a resurfacing system instead of just a coating.
This approach adds a new layer of material, which can then be stained, sealed, or polished. Great for patios, walkways, or interiors where you want a decorative finish.
Still cheaper and faster than replacement, and far more customizable.
The Bottom Line
Replacing concrete? You’re paying more and waiting longer.
Coating or resurfacing? You’re saving money and getting better performance.
At Orr Floor Care, we price every job based on square footage, prep level, and the type of system we’re installing. No bait-and-switch quotes. No mystery add-ons.
If your floor’s driving you nuts but doesn’t need to be torn out, we’ll give you a realistic, honest breakdown of your options—and make sure you’re getting long-term value.
Next up, we’ll walk you through exactly what to expect when you hire a pro to coat or resurface your floor—from prep to final finish.
What to Expect from a Professional Coating or Resurfacing Job
If you’ve never had a floor professionally coated or resurfaced, you might be wondering: what’s the process actually look like? Is it messy? How long does it take? Will my garage or patio be out of commission for days on end?
Let’s walk through a typical Orr Floor Care project—from first contact to final walkthrough.
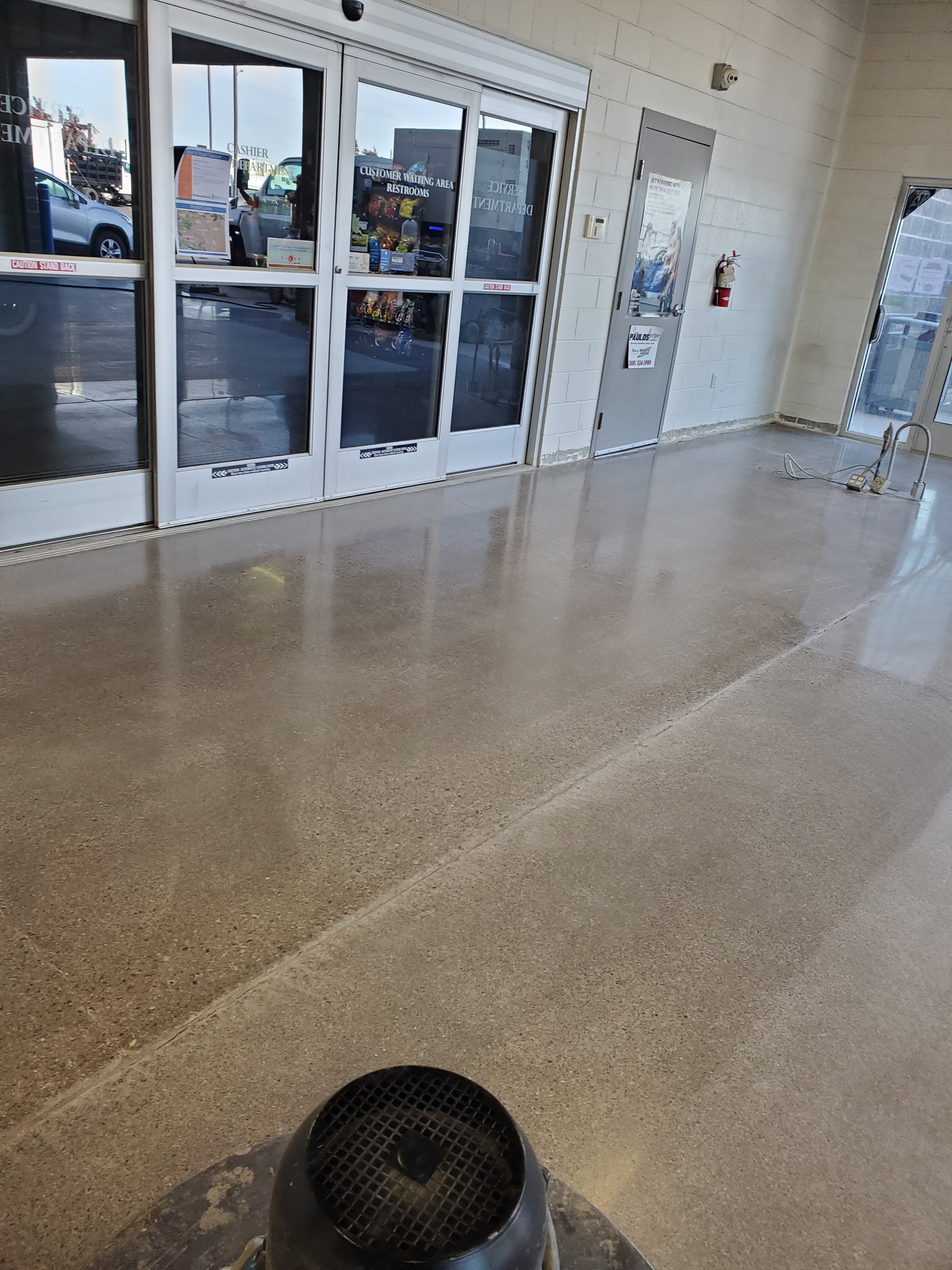
Step 1: On-Site Evaluation & Quote
It all starts with a quick site visit. We take a look at your concrete, check for cracks, test for moisture, and assess the overall condition. Then we talk about your goals—are you going for a showroom-style epoxy floor? Need to fix pitting? Want a decorative overlay for your patio?
Once we know what you’re after and what we’re working with, we give you a no-pressure quote, customized to your space. No generic pricing. No upselling nonsense.
Step 2: Surface Prep
This is where the pros separate themselves from the weekend warriors.
Every project begins with mechanical diamond grinding—not acid etching, not sanding, but serious surface prep that opens up the pores of the concrete so the coating or resurfacer bonds properly.
We also:
Fill cracks and joints with flexible filler
Patch low spots or damaged areas
Vacuum and clean thoroughly
Moisture test if needed (especially for basements or slab-on-grade interiors)
Step 3: System Installation
Depending on the system you’ve chosen, the installation process can include:
Base coat application
Decorative broadcast (flakes, quartz, or metallic pigments)
Scraping and vacuuming (for flake systems)
Topcoat application with polyaspartic or urethane for added durability
If you’re going with a resurfacing overlay, we’ll trowel or spray the microtopping, finish the surface texture, and apply stains or sealers as needed.
Step 4: Cure & Return to Service
Most epoxy and polyaspartic systems are walkable within 24 hours and ready for light traffic in 48–72. Compare that to the 28-day cure time for a new slab and it’s no contest.
For resurfaced patios or walkways, it’s usually safe to walk on by the next day—again, weather depending.
Step 5: Final Walkthrough
We don’t leave until you’re happy. We’ll walk the project with you, go over care and cleaning tips, and make sure everything meets expectations. We stand behind every floor we install.
So what should you expect from a professional coating or resurfacing job in Twin Falls? Efficiency, transparency, and long-term performance. No gimmicks. No shortcuts. Just solid work that speaks for itself.
How Orr Floor Care Helps Twin Falls Homeowners Upgrade Smart
At Orr Floor Care, we don’t just coat concrete—we restore it, protect it, and elevate it. We’ve helped hundreds of homeowners across Twin Falls, Jerome, Burley, Kimberly, Filer, and other nearby Idaho communities transform worn-out slabs into durable, great-looking surfaces they can actually be proud of.
Our goal isn’t to sell you something you don’t need. It’s to help you make a smart, informed decision that fits your space, your budget, and your long-term goals.
Why Homeowners Trust Orr Floor Care
We’re Local. We live here. We work here. We know what Twin Falls weather does to concrete, and we know how to protect against it.
We Don’t Use Outside Crews. Every job is done by our in-house team—no subcontractors, no cutting corners.
We Prep Right. It doesn’t matter how good the coating is if the prep is wrong. We invest in the right equipment, follow industry-best standards, and never rush the foundation work.
We Offer Options. Not every slab needs the same treatment. We’ll explain the differences between epoxy, polyaspartic, overlays, polishing, sealing—you name it—and help you pick what works.
Whether your garage floor is dusty and cracking, your patio’s seen better days, or your basement needs a more functional finish, we’ve got the tools and the experience to get it done right.
If the concrete needs to be replaced, we’ll tell you. But if it doesn’t? We’ll show you how to bring it back to life—better than new.
The next move is yours.
Ready to Upgrade Smarter? Let’s Talk.
If your concrete is starting to show its age, don’t assume replacement is your only option.
Whether you’re dealing with cracks, stains, surface wear, or just a floor that looks tired, Orr Floor Care is here to help you upgrade without the hassle of a full demo. We’ll evaluate your slab, walk you through the options, and recommend the solution that gives you the best long-term value—no fluff, no sales pressure.
We serve Twin Falls, Jerome, Burley, Kimberly, Filer, and surrounding Idaho communities with coatings, resurfacing, polished concrete, and full restoration services.
Call us today at (208) 404-6679 or shoot us an email at [email protected] to schedule your free quote. Let’s make your concrete floor something worth showing off.