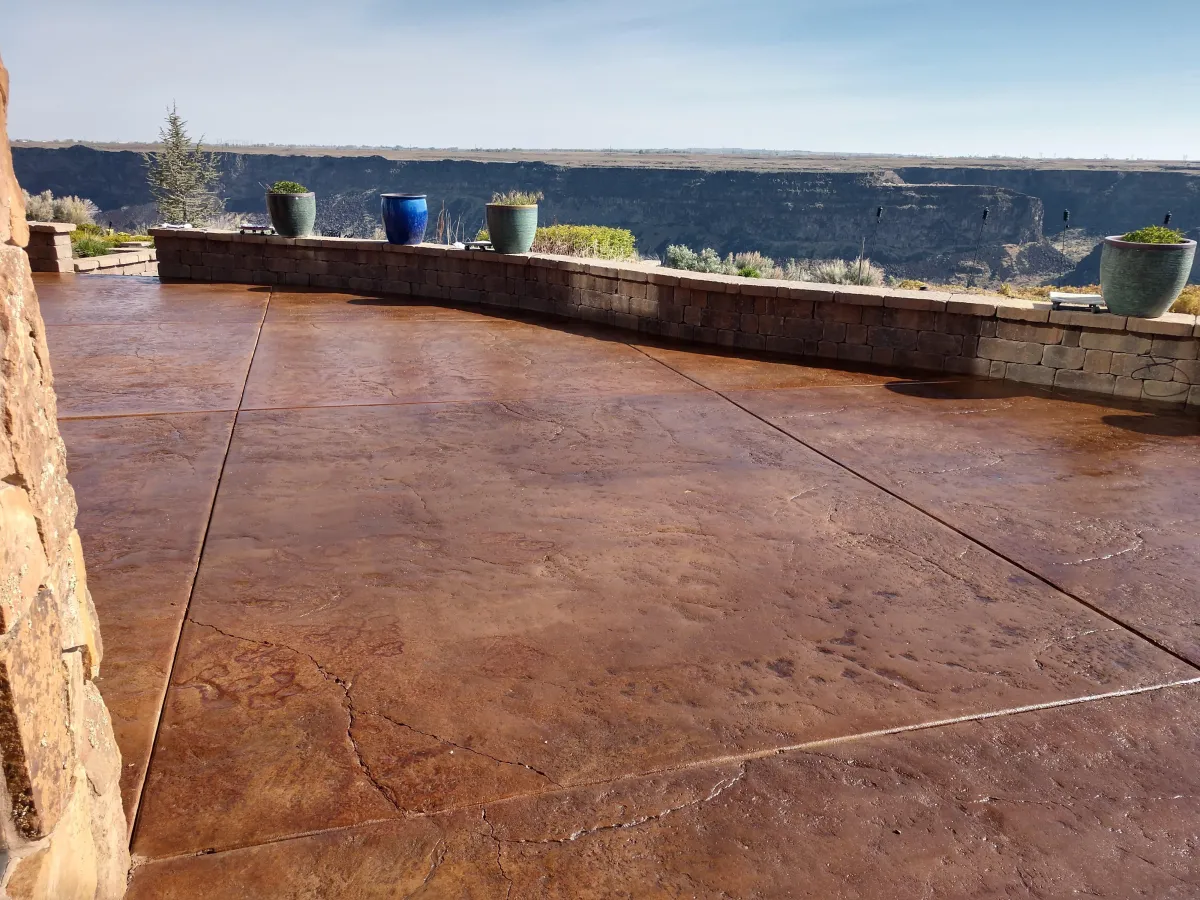
5 Decorative Concrete Trends Taking Over Twin Falls in 2025
Concrete isn’t what it used to be—and that’s a good thing. In 2025, decorative concrete is stepping out of the shadows and into the spotlight across Twin Falls, with homeowners, contractors, and business owners ditching bland gray slabs in favor of bold, stylish, and high-performance finishes. From matte-polished floors that scream modern elegance to flake epoxy coatings built to outlast Idaho winters, today’s concrete does more than support your space—it defines it. At Orr Floor Care, we’re right in the thick of it, helping Twin Falls clients ride the wave of innovation without compromising on durability, function, or long-term value.
Table of Contents:
5 Decorative Concrete Trends Taking Over Twin Falls in 2025
Integrating Color and Custom Patterns in Interior Decorative Concrete Floors
How ORR Floor Care Helps Twin Falls Clients Stay Ahead of the Cure
TL;DR: Decorative Concrete Trends Taking Over Twin Falls in 2025
Matte-polished concrete is replacing high-gloss finishes for a more natural, modern look with low maintenance.
Stamped and textured overlays are mimicking stone, wood, and brick—without the price or upkeep of real materials.
Flake epoxy flooring is dominating garages and workshops for its durability, grip, and clean, professional appearance.
Concrete resurfacing is giving old, cracked slabs a second life—faster and cheaper than full replacement.
Interior concrete floors are going bold with color, scoring, and custom patterns—perfect for kitchens, basements, and commercial spaces.
Want a floor that looks incredible and actually lasts? Call Orr Floor Care at (208) 404-6679 or email [email protected] to get started.
Trend #1: The Rise of Matte-Polished Concrete Finishes
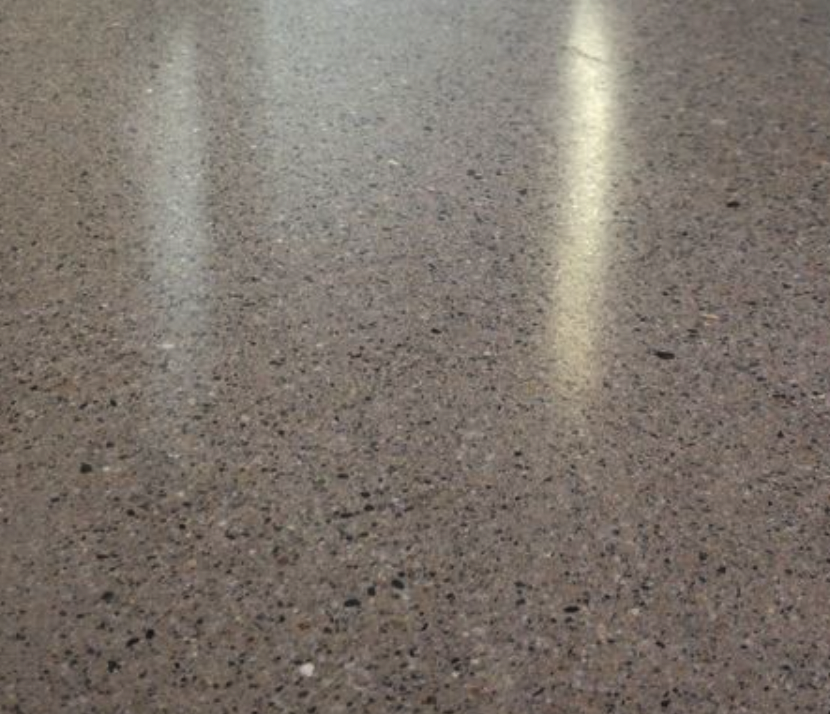
High-gloss concrete floors had their moment—but in 2025, the design world is leaning into something a little more grounded: matte-polished concrete. If you’re imagining dull and dusty, think again. These finishes are sleek, soft-looking, and refined without screaming for attention. And here in Twin Falls, more homeowners and business owners are choosing matte not just for its looks, but for the livability.
Why Matte Is the New Gloss
You know that showroom shine you see on ultra-polished concrete floors? It looks incredible in a lighting store or high-end dealership—but in a living room or office, it can feel like overkill. Matte-polished concrete has a lower reflectivity, which makes it easier on the eyes and creates a warmer, more natural atmosphere. It’s subtle, sophisticated, and timeless—which is exactly what many Idaho property owners are going for in 2025.
Here’s the kicker: you still get all the performance benefits. The surface is just as dense and hardwearing as high-gloss finishes. The difference is in the final grit and polishing stage—we stop a little earlier in the process to achieve a low-sheen surface that still resists stains, traffic, and abrasion.
Where It’s Showing Up in Twin Falls
We’re seeing matte-polished concrete pop up all over town:
Modern homes with open floor plans love it for the cohesive, continuous feel.
Restaurants and coffee shops are using it to warm up industrial interiors.
Retail spaces and offices choose it for its low-maintenance, non-slip characteristics.
Here’s a real example: One of our recent clients in Twin Falls renovated a downtown commercial space that used to have tile. We came in, removed the glue and old surface coatings, polished the concrete to a soft matte finish, and sealed it. Now it’s the anchor feature of the space—and it holds up like a champ to daily foot traffic.
Performance Without the Glare
One common concern with polished concrete has always been reflectivity—especially in rooms with a lot of windows or overhead lighting. Glossy floors can create harsh glares and hot spots that aren’t great for productivity or comfort. Matte finishes eliminate that issue entirely.
And don’t confuse matte with porous or unsealed. At Orr Floor Care, we still densify and seal every matte-polished floor. You’re getting the same stain resistance, abrasion protection, and ease of cleaning. It just doesn’t have that “wet look” shine. Functionally, it’s still concrete flooring at its best—you’re just choosing a softer aesthetic.
Low Maintenance, High Style
Here’s something every property owner can appreciate: matte-polished concrete is incredibly easy to maintain. There’s no wax to reapply. No gloss to buff back up. Just basic sweeping and occasional mopping. Plus, because matte finishes hide scuffs and dust better than high-gloss surfaces, they stay looking clean longer between touch-ups.
For folks in Twin Falls who don’t want to baby their floors, this is a huge win.
How It’s Done: A Quick Behind-the-Scenes Look
To achieve a high-quality matte-polished finish, we follow a multi-step mechanical grinding and polishing process. This isn’t a quick DIY job—it’s a professional system designed for both performance and aesthetics. Here's how it breaks down:
Surface Prep – We begin by mechanically grinding the floor with coarse diamond tooling to remove any coatings, adhesives, or surface imperfections. This is where we fix spalling, patch cracks, and create a level base to work from.
Honing – After the initial grind, we move into the honing stages using medium-grit diamonds—typically in the 50–200 grit range. This step smooths the surface, refines the texture, and eliminates the deep scratch patterns left by coarse prep. Honing is critical for matte finishes because it allows us to create a clean, even canvas without over-polishing.
Densification – Once the floor is honed, we apply a liquid densifier that penetrates the surface and chemically reacts with the concrete to harden it from within. This boosts abrasion resistance, reduces dusting, and helps the floor stand up to heavy foot traffic and cleaning over time.
Progressive Polishing – From there, we continue with finer diamond grits—usually stopping at 400 or 800 grit, depending on how matte or satin the client wants the finish. We’re not chasing a mirror shine here; we’re aiming for a soft, natural glow with just enough refinement to feel smooth underfoot.
Sealing – Finally, we lock it all in with a penetrating sealer that protects against moisture, oil stains, and everyday wear. Unlike topical coatings, this sealer doesn’t add gloss—it just reinforces durability while keeping the floor breathable and easy to maintain.
The Orr Floor Care Difference
Not all matte-polished concrete jobs are created equal. It’s easy to cut corners—stop polishing too soon, skip proper densification, or use cheap sealers—and end up with a floor that looks dull and wears out fast.
At Orr Floor Care, we don’t play that game. Our team is trained to do things right, from the initial prep to the final polish. Whether it’s a single-family home in Filer or a commercial upgrade in downtown Twin Falls, we treat each floor like it’s going to represent us for the next 20 years—because it will.
Trend #2: Textured Concrete That Mimics Natural Stone or Wood
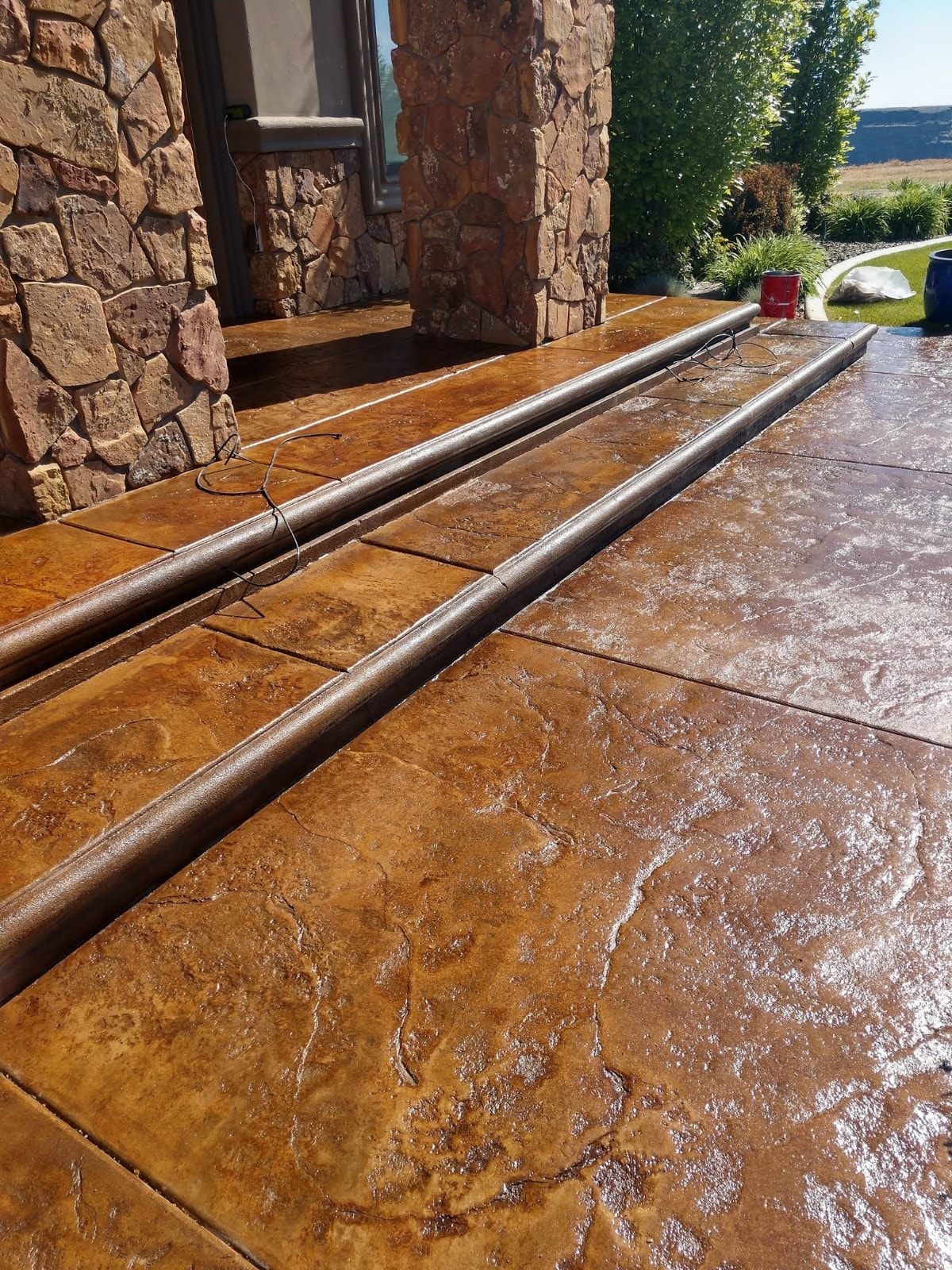
When you think of concrete, most people picture something flat, gray, and industrial-looking. But in 2025, that image is long gone—especially in Twin Falls, where textured and patterned decorative concrete is making a serious splash. These finishes look like natural stone, slate, brick, or even reclaimed wood—but they’re still concrete under the surface. And that’s what makes them so smart.
Why This Trend Is Gaining Ground in Twin Falls
People want beauty and practicality. That’s exactly what this trend delivers.
We’re talking about stampable overlays, hand-troweled textures, and custom stains that allow us to replicate the look of flagstone, cobblestone, hardwood planks, or travertine—at a fraction of the price of the real materials. You still get the durability and low maintenance of concrete, but with an upscale, customized finish.
It’s perfect for:
Patios and pool decks that need slip resistance and weather durability.
Driveways where homeowners want more than plain gray curb appeal.
Commercial walkways and entryways that need to impress without constant upkeep.
And it’s not just a surface-level thing. The textures are built into the overlay, which bonds directly to the existing concrete slab. That means you’re not laying tile or stone that can crack, shift, or heave during Twin Falls’ seasonal freeze-thaw cycles. You’re upgrading your surface without replacing it.
Popular Styles We’re Seeing in 2025
Every year, we get a new wave of style requests. Here’s what’s dominating this year in the Twin Falls market:
🔸 Wood Plank Concrete
Yes, you read that right. Concrete that looks like weathered barn wood or wide oak planks. Using a combination of stamping mats, custom staining, and fine detailing, we can create floors that have wood grain texture and realistic knot patterns—without ever worrying about water damage or termite issues.
🔸 Flagstone & Slate Textures
Stamped overlays that mimic natural flagstone are huge for outdoor living areas. We often stain or tint them in earthy tones—sandstone, charcoal, rust—to give that authentic, aged-stone look. Great for rustic patios, walkways, and restaurant patios.
🔸 Brick Patterns with Antique Finishes
For clients who want a vintage vibe, we use stamping or scoring to create brick patterns, then layer stain to give it a warm, timeworn appearance. Think historical downtown charm without the maintenance nightmare of real brick.
Why It Works So Well in Idaho
Twin Falls has a unique mix of modern tastes and rugged outdoor lifestyle. Homeowners and businesses here want surfaces that feel connected to nature, that blend with Idaho’s landscape, and that don’t buckle under snowmelt, dust, or sun exposure.
Concrete that mimics stone or wood fits the bill beautifully. It won’t warp in the summer or crack in the winter if installed properly. It handles dust, mud, and foot traffic like a champ. And it doesn’t demand the upkeep of grout lines, wood refinishing, or natural stone sealing.
Plus, these overlays can be resurfaced over time if clients want to change the color or pattern down the road—much more flexible than traditional materials.
From Budget to High-End: It’s Scalable
One of the best things about this trend? It can scale based on budget.
Basic stamped overlays with a single color stain are perfect for someone looking for a quick, affordable driveway or patio upgrade.
High-end multi-layered textures with hand-cut joints, multi-tone stains, and custom antiquing are ideal for commercial properties or luxury homes looking to make a statement.
At Orr Floor Care, we help clients navigate what level of customization makes the most sense for their goals—and their budget.
What to Watch Out For (Pro Insight)
Now, let’s be honest. There’s a lot of bad stamped concrete out there. We’ve seen projects where patterns were misaligned, textures were inconsistent, or stain application looked like it came out of a spray can. The difference between “Wow” and “What happened?” comes down to the installer.
Here’s what we do differently:
We use high-quality stamp mats and tools—not cheap knockoffs.
We layer color intentionally—not with a one-size-fits-all dye.
We seal properly to lock in the look and ensure it performs.
If someone’s quoting a job at half the normal price, it usually means they’re skipping steps or using budget materials. And that shortcut always shows later on—usually in the form of early cracks, fading, or lifting overlays.
What It Costs (and Why It’s Worth It)
Textured decorative concrete is one of those rare upgrades where you get both curb appeal and ROI. It adds visual impact without the high installation or maintenance cost of premium materials. Plus, the long-term durability keeps your investment looking good for years.
On average, you’re looking at:
$8–$15 per square foot for most stamped or textured overlay systems.
Compared to $18–$35 per sq ft for stone or $12–$20 for pavers, it’s a smart move.
Textured concrete has come a long way from the basic “builder-grade” patterns of the early 2000s. In 2025, this trend is about realistic replication, style flexibility, and long-term durability. Twin Falls homeowners are realizing that you don’t need imported slate or exotic wood to get a beautiful, resilient surface—you just need the right team to bring your concrete to life.
Trend #3: Flake Epoxy Flooring for Garages and Workshops
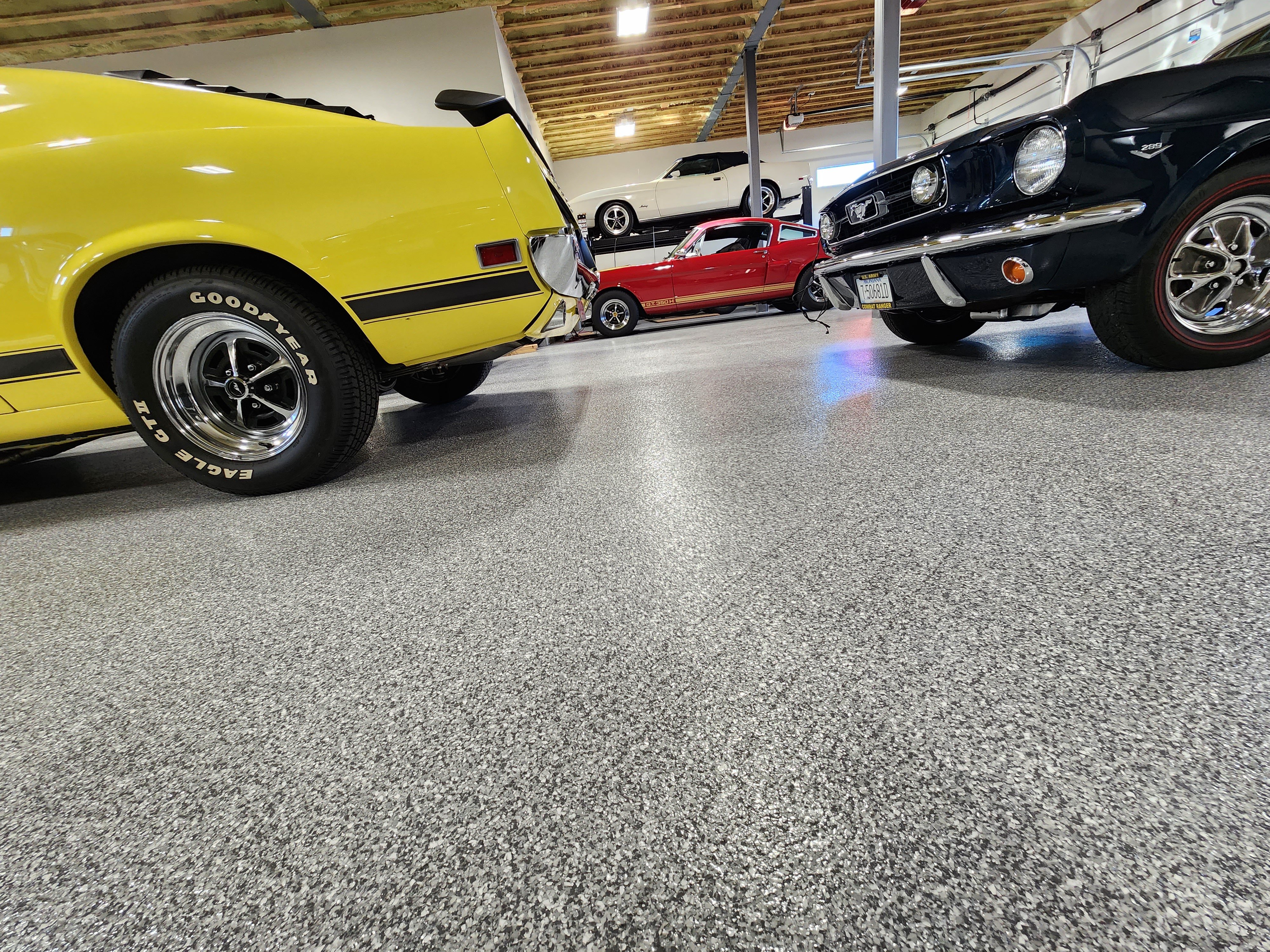
Gone are the days when garages were dusty, cracked, and forgotten zones. In 2025, flake epoxy flooring is turning utilitarian spaces into polished, high-performance environments—literally. Whether you're parking your truck, welding gear, or just want a garage floor that doesn’t look like it’s been through three Idaho winters (because it probably has), flake epoxy is the go-to solution in Twin Falls.
What Is Flake Epoxy Flooring, Exactly?
Let’s break it down. Flake epoxy systems are multi-layered flooring systems that start with a solid epoxy or polyaspartic base coat. Into that base, we broadcast decorative vinyl flakes—those little colored chips that create texture, pattern, and grip. Once the flakes are set, we lock everything in with a clear topcoat, usually a high-performance urethane or polyaspartic sealer.
What you’re left with is a floor that looks sharp, hides dirt like a champ, and laughs in the face of hot tires, dropped tools, and oil stains.
Why It’s Blowing Up in Twin Falls
This trend isn’t just about looks—it’s about lifestyle. Here’s why local homeowners and shop owners are all over flake epoxy this year:
Durability: We’re talking 3–5 layers of industrial-grade protection that stands up to real abuse—vehicle traffic, chemical spills, power tools, you name it.
Safety: The flake texture adds slip resistance, which is huge during wet or icy months.
Cleanability: Dust and grime don’t stick to a sealed epoxy surface. Just sweep or hose it off.
Style Options: With a huge range of flake blends—from neutral stone-look tones to bold custom colors—clients can match the floor to their space.
Fast Turnaround: Many garage floors can be done in just 1–2 days, depending on the system we use.
Who’s Using It? (Spoiler: It’s Not Just Car Guys)
You’d be surprised how many different clients are asking for flake epoxy these days. Here’s a breakdown of where it’s going in Twin Falls:
Residential Garages: The #1 spot. People want their garages to match the rest of their home—clean, sharp, usable.
Workshops & Hobby Spaces: Mechanics, welders, woodworkers—this floor holds up.
Commercial Auto Shops & Warehouses: Oil resistance, slip protection, and a professional look for customer-facing areas.
Mudrooms & Laundry Rooms: It’s creeping indoors, especially in farm homes or properties where people want durability over décor.
We even had a client recently who runs a small outdoor gear rental shop. We installed flake epoxy in his back storage area to handle all the dropped boots, wet skis, and gear abuse—and he’s already called us to quote the showroom floor next.
What Makes a Flake Epoxy System So Tough?
This isn’t just paint. A proper flake epoxy floor is a chemically bonded system. Here’s what we use at Orr Floor Care:
Diamond grinding to prep and profile the concrete.
100% solids epoxy base coat for strength and adhesion.
Full broadcast of color flake—not a light sprinkle. Full broadcast = full coverage and better texture.
Scrape and clean to remove loose flakes and level the surface.
Clear topcoat of polyaspartic or urethane for chemical resistance, UV stability, and gloss (or satin, depending on your style).
The result is a floor that lasts 15–20+ years under typical use—and even longer in lower-traffic areas.
Flake Epoxy vs. Plain Epoxy: Why the Flakes Matter
Some people ask, “Can I just get regular epoxy without the flakes?” Technically, yes. But here’s what they miss:
Plain epoxy shows everything—every smudge, every scratch, every tire mark.
Flake blends camouflage wear and tear, which is a big win if you’re actually using your garage or shop.
Flakes add texture, which = traction. Smooth epoxy can get slippery when wet. That’s a safety hazard, especially in Idaho winters.
So while plain epoxy has its place in industrial or warehouse settings, flake systems are king for residential and small commercial clients who want a balance of looks and toughness.
Design Options That Fit Any Vibe
This isn’t a one-style-fits-all product. Flake epoxy is insanely customizable:
Neutral tones (grays, tans, charcoals) for a clean, modern look.
Stone blends that mimic granite or quartz for a natural aesthetic.
High-contrast colors for businesses or auto shops that want a bold, branded vibe.
And because we can adjust flake size—from microchips to 1/4" broadcast—you can fine-tune the texture and appearance. It’s design-forward without sacrificing performance.
Pricing and Value in 2025
In 2025, flake epoxy is still one of the best bang-for-your-buck flooring options on the market.
Average price in Twin Falls: $6–$9 per sq ft for residential garages. Commercial or heavy-duty applications may go higher depending on coating thickness and topcoat type.
Compare that to tile or high-end vinyl? Flake epoxy wins on durability, chemical resistance, and longevity every time.
Plus, it increases usable square footage and adds value to the home. We’ve had realtors call us to ask what kind of floor coating we used in a listing—it stands out.
Bottom Line: It’s More Than Just a Pretty Floor
Flake epoxy isn’t about making your garage look nice (though it does that too). It’s about creating a long-lasting, functional, and professional-grade surface that you don’t have to babysit. If you’re someone who actually uses your space—whether you’re a weekend mechanic, a snowmobile enthusiast, or just tired of concrete dust—this is the upgrade you need.
And when it’s installed by a pro crew like Orr Floor Care, you’re not just getting a coating—you’re getting a system built to last.
Trend #4: Decorative Concrete Resurfacing Instead of Full Replacement
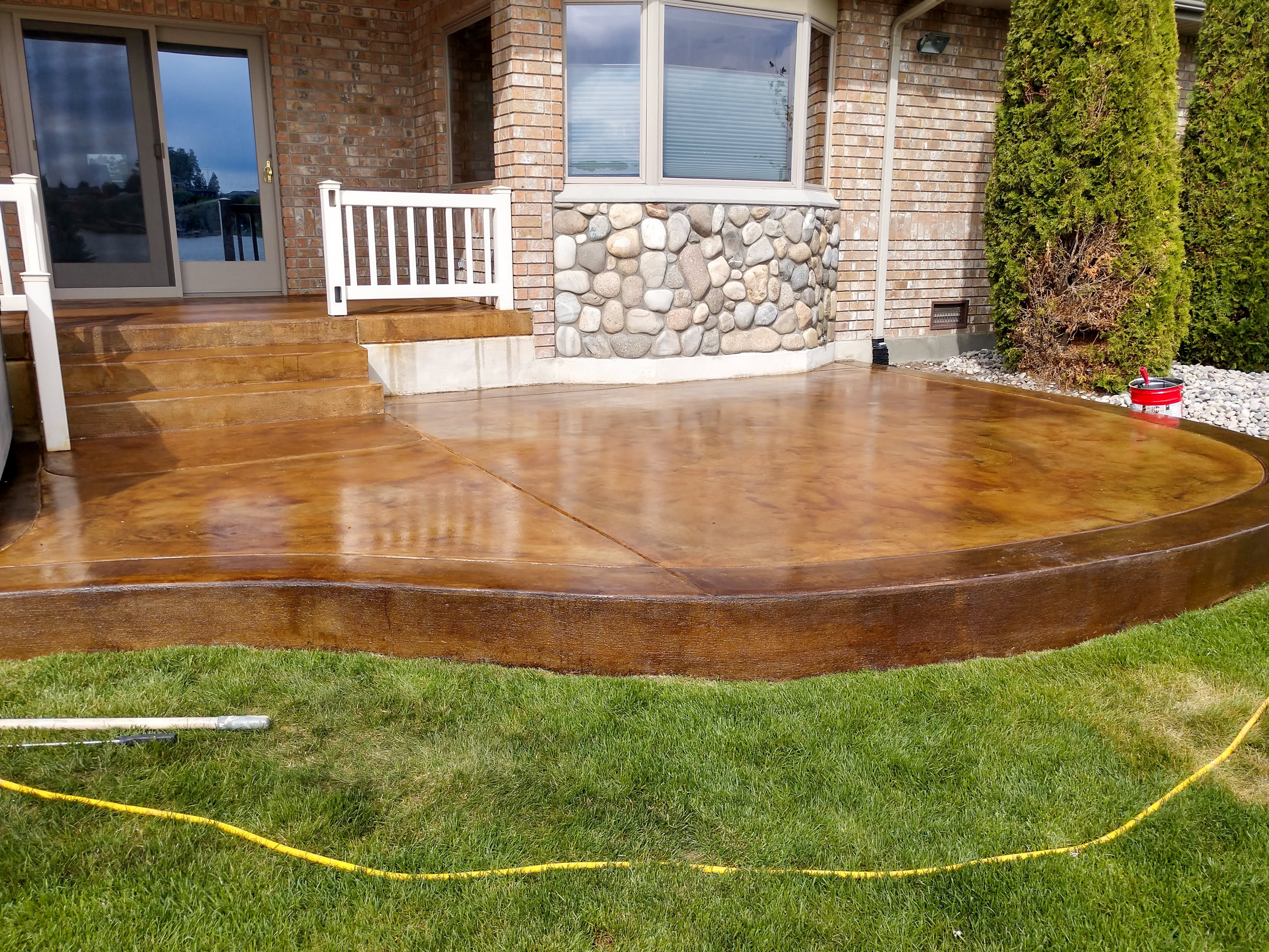
Here’s the deal: full concrete replacement is expensive, messy, and usually overkill. That’s why in 2025, more homeowners and businesses in Twin Falls are skipping the jackhammers and going for something smarter—decorative concrete resurfacing.
Whether it’s a weathered patio, an oil-stained driveway, or a garage floor that’s seen better days, resurfacing gives old concrete a new lease on life—without the cost and downtime of demolition. And when it’s done right, it doesn’t just cover up damage—it transforms the look and feel of your space entirely.
What Exactly Is Concrete Resurfacing?
Think of it like a facelift for your concrete. Resurfacing involves applying a thin, high-performance overlay directly on top of an existing slab. Once cured, that overlay becomes the new surface—and it can be customized with texture, color, stain, polish, or pattern.
Here’s what that looks like in real-world terms:
That cracked, sun-faded pool deck? It can be skimmed, textured, and stained to look like stone or tile.
The garage with surface pitting? We can patch, grind, and top it with a flake epoxy system.
That entryway with mismatched patches and old repairs? We resurface it smooth and add a custom stain for a modern, uniform look.
The underlying concrete still does the heavy lifting, but the new surface boosts appearance, performance, and property value in one shot.
Why It’s Catching On in Twin Falls
Let’s face it—Twin Falls weather is rough on concrete. Between winter freeze-thaw cycles, dry dusty summers, and the occasional heavy load from trucks or equipment, most outdoor slabs around here start showing wear after 5–10 years.
But here’s the thing: most of those slabs don’t need to be replaced. They’re structurally sound—they just need a surface upgrade. And that’s where resurfacing comes in.
For Twin Falls homeowners, it’s a no-brainer:
Faster turnaround: Most resurfacing projects take 1–3 days vs. a week or more for a full pour.
Lower cost: You skip demo, disposal, and heavy machinery.
Custom aesthetics: You’re not stuck with boring gray—you can stain, stamp, or polish the new surface.
And for commercial properties? It’s even better. You can refinish walkways, entryways, or lobbies with minimal disruption to operations.
Common Use Cases We’re Seeing in 2025
We’re resurfacing everything from driveways to retail showrooms. Here are the biggest requests right now in the Twin Falls area:
Driveways: Cracked, spalled surfaces are getting textured overlays and new stain colors—massive boost in curb appeal.
Patios: Outdated broom-finished slabs are resurfaced with hand-troweled finishes and warm, earthy color tones.
Commercial walkways: Businesses are replacing chipped concrete paths with stamped finishes that mimic slate or flagstone.
Warehouse interiors: Resurfacing with polishable overlays to create dust-free, low-maintenance floors that stand up to traffic.
One of our favorite recent projects? A homeowner in Kimberly had a 20-year-old back patio that was flaking and uneven. We ground it down, applied a resurfacing overlay with a sandstone texture, then came back with a custom two-tone stain. They told us afterward it looked like they got a whole new backyard—and at a third of the price of replacement.
What’s the Process Like?
Good resurfacing isn’t a band-aid—it’s a system. Here’s how we do it at Orr Floor Care:
Evaluation: First, we inspect the existing slab. If it’s cracked all the way through or severely broken, we’ll tell you straight-up—it may not be a good candidate. But if the issues are mostly surface-level? You’re golden.
Surface Prep: We grind off old coatings, clean the slab, and fix any minor cracks or pitting. This is where many low-budget contractors skimp—and it’s why their overlays fail early.
Overlay Application: We apply a cementitious or polymer-modified overlay, customized based on your needs (thin skim coats for smooth finishes, thicker textures for stamped designs).
Design & Color: After curing, we stain, seal, or polish the surface to achieve the final look. Clients can choose natural tones, bold colors, or faux finishes that mimic tile, wood, or stone.
Sealing: The final step is a penetrating or topical sealer that locks in the appearance and protects from UV, stains, and moisture.
Resurfacing vs. Replacement: The Smart Choice
Let’s break it down in numbers. Full concrete replacement can run $12–$20 per square foot when you factor in demo, disposal, forming, pouring, finishing, and curing. Resurfacing? You’re usually looking at $6–$10 per square foot, depending on the system.
That means:
Less disruption to your home or business.
Faster turnaround.
Lower cost.
More design flexibility.
And the performance? When done right, resurfaced concrete lasts 10–15 years or more, especially when regularly sealed and maintained.
Performance Matters—So Does the Installer
Here’s where we give it to you straight: not all resurfacing is created equal. We’ve been called in more than once to fix jobs where overlays were peeling, cracking, or completely delaminating within a year. Why? Usually because:
The surface wasn’t properly prepped.
The overlay wasn’t bonded correctly.
The contractor rushed the cure or used cheap materials.
At Orr Floor Care, we don’t cut those corners. We use industrial-grade resurfacing products, tailored for Idaho’s climate, and we prep the slab the right way, every time. If the slab isn’t a good candidate? We’ll tell you. If it is? We’ll make it look brand new.
Design Flexibility: You’re Not Stuck with “Concrete Gray”
This is where resurfacing shines. You can turn a drab surface into just about anything:
Stained overlays in rich browns, reds, charcoals, or custom blends.
Stamped textures like slate, ashlar, or even wood grain.
Polished micro-toppings for a clean, modern look.
Matte or gloss finishes depending on where and how you’ll use it.
And because we’re working with a fresh canvas, you have full control over the aesthetic—without needing a brand-new slab.
If your concrete is structurally sound but looks like it’s been through a few rodeos (because, well, it has), resurfacing could be the smartest upgrade you make this year.
Trend #5: Integrating Color and Custom Patterns in Interior Concrete Floors
Concrete has officially moved indoors—and not just in ultra-modern lofts or minimalist homes. In 2025, homeowners and businesses in Twin Falls are embracing colored and patterned decorative concrete as a smarter, more stylish alternative to tile, hardwood, or vinyl. We’re seeing it in kitchens, basements, retail spaces, offices—you name it.
The best part? This isn’t just about making concrete look better. It’s about customizing your space without sacrificing the durability that concrete is known for.
Why Interior Concrete Is Getting a Design-Forward Makeover
Let’s face it: floors take a beating. Between foot traffic, furniture, spills, and everything in between, most flooring options eventually show their age. Hardwood scratches. Tile grout stains. Vinyl curls. But a well-finished decorative concrete floor? It holds up like a champ.
That’s why more clients are asking us to help them personalize their interior concrete with color treatments, scoring, saw cuts, and stenciled patterns that take it from builder-basic to completely custom.
It’s a trend that hits all the right notes:
Design flexibility – No two floors have to look the same.
Long-term durability – The surface doesn’t fade, peel, or warp.
Low maintenance – No grout, no waxing, no refinishing every few years.
Eco-friendliness – Often installed over existing slabs—no extra materials needed.
How Color Is Being Used in 2025
When people think of colored concrete, they usually picture bold red patios or orange-stained driveways from 15 years ago. But that’s not where this trend is headed.
Today’s coloring techniques are more sophisticated and subtle. In Twin Falls homes and commercial interiors, we’re seeing a shift toward earthy tones, smoky charcoals, and layered stains that add depth and warmth without feeling fake or overdone.
Here’s what’s trending now:
Water-based stains for soft, natural hues—especially popular in residential living spaces and basements.
Acid-based stains for rich, variegated tones that mimic stone or leather.
Tinted sealers that enhance the surface color without overpowering the natural texture of the concrete.
We recently completed a stained concrete floor in a modern farmhouse-style home just outside Twin Falls—warm beige base tone, with subtle charcoal marbling and a satin finish. The homeowner was blown away at how “non-concrete” it felt—yet it still delivered all the durability she needed with three kids and a couple of dogs.
Custom Patterns That Add Personality Without the Fuss
This is where it gets fun. With decorative saw cuts, score lines, stencils, and templates, we can create patterns that break up large spaces or simulate the look of tile, stone, or even inlaid rugs.
Clients are getting more creative with layouts:
Geometric grids that mimic oversized tile without the grout.
Borders and banding to define rooms in open floor plans.
Logo stencils in commercial spaces or branded showrooms.
Freeform organic shapes for artistic, one-of-a-kind statement pieces.
Unlike tile or wood planks, there’s no risk of delamination, cracking grout, or shifting seams. It’s all carved directly into the concrete surface and sealed for longevity.
Interior Applications We’re Seeing in Twin Falls
Concrete used to be reserved for garages and basements. That’s no longer the case. In 2025, indoor decorative concrete is a design choice, not a compromise—and here’s where it’s showing up:
Kitchens: Especially in modern or industrial-style homes. Add radiant heating and it’s unbeatable.
Basements: Perfect for moisture-prone spaces. Can be stained, sealed, or polished.
Entryways: Durable enough for high traffic and weather drag-in. Easy to clean.
Retail and office interiors: Adds a high-end look with commercial-grade resilience.
Airbnb or rental properties: Easy to maintain between guests, no flooring repairs needed.
And we’re seeing more renovation clients pull out carpet or LVP and opt for polished, stained concrete underneath—especially when they discover they already have a good slab in place.
Sealing: The Final (and Most Crucial) Step
With interior decorative concrete, sealing isn’t optional—it’s mission critical.
We use penetrating sealers for matte finishes or urethane/polyaspartic coatings for higher gloss and durability. The right sealer:
Protects the color and design from fading
Makes cleaning a breeze (no waxes or special cleaners needed)
Provides a layer of resistance against moisture and spills
Pro tip: in kitchens or bathrooms, we often recommend a satin-finish polyurethane that offers the right balance of sheen and protection—no slippery surface, no dull appearance.
Is It Cheaper Than Tile or Hardwood? Usually—But It’s Also Smarter
The cost for interior decorative concrete floors depends on the level of customization, but it typically falls in this range:
$7–$12 per square foot for stained or patterned overlays
$10–$15 per square foot for polished concrete with decorative cuts or color
Much less long-term maintenance than tile, wood, or vinyl
And you’re getting a monolithic floor—no seams, no joints, no transitions. Just one continuous surface that looks incredible and performs even better.
Design That Lasts, Floors That Don’t Flinch
Whether it’s a home in Filer, a commercial space in downtown Twin Falls, or a weekend cabin out near Murtaugh, colored and patterned interior concrete is proving it can do it all. It holds up to pets, kids, furniture, moisture—you name it—and still looks amazing years down the road.
And when you work with Orr Floor Care, you're not getting a cookie-cutter system. You're getting a floor that fits your space, your lifestyle, and your taste.
How Orr Floor Care Helps Twin Falls Clients Stay Ahead of the Curve
At the end of the day, decorative concrete isn’t just about what’s trending—it’s about choosing the right system, installed the right way, by the right people. That’s where Orr Floor Care comes in. We’re not a national chain. We’re not here to churn out cookie-cutter jobs and call it good. We’re a locally owned, family-operated concrete flooring contractor, and our name is on every floor we touch.
When Twin Falls clients call us, they’re not just looking for another contractor—they’re looking for a partner. Someone who knows the climate, the construction challenges, the product systems, and how to tailor a solution that works for your space, your budget, and your timeline.
What Sets Us Apart
Here’s what makes working with Orr different from your average concrete guy with a Home Depot grinder:
🔹 True Surface Prep
We don’t skip steps. Every project starts with the right mechanical prep—grinding, cleaning, patching, and moisture testing. It’s the difference between a floor that lasts 20 years and one that peels in 12 months.
🔹 Product Knowledge
We’re trained in polished concrete systems, flake epoxy flooring, resurfacing overlays, and sealing methods. We don’t just know how to install it—we know when it works, when it doesn’t, and how to specify the right finish for the space.
🔹 Design Insight
Trends are only valuable if they actually make sense in your home or business. We’ll walk you through color blends, texture options, finish levels, and long-term care—not just to make it look good, but to make sure it fits your lifestyle and use case.
🔹 One-on-One Service
When you call us, you talk to a real person—usually one of the owners. We’re on-site, we answer our phones, and we stand by our work.
Who We Work With
We serve a wide range of clients across Twin Falls and the surrounding areas, including:
Homeowners renovating garages, basements, patios, and kitchens
Contractors and builders looking for reliable decorative concrete subcontractors
Business owners upgrading showrooms, storefronts, and industrial spaces
Property managers who need durable, low-maintenance solutions for rentals or multi-unit properties
Big job or small—we bring the same level of attention, expertise, and integrity.
Our Core Services Include:
Polished Concrete Flooring – From matte to high-gloss, customized for residential and commercial interiors.
Concrete Resurfacing – Overlays, repairs, and refinishing that bring worn-out slabs back to life.
Decorative Concrete Finishes – Staining, scoring, stamping, and custom textures.
Epoxy Floor Coatings – Including flake epoxy flooring systems for garages and commercial use.
If it’s concrete, and it needs to look good and last—we’ve got you covered.
Let’s Design Something That Lasts – Contact Orr Floor Care
If you’ve been thinking about upgrading your concrete—don’t wait until another season of snow, dust, or driveway cracks sets in. Whether it’s your garage, your patio, your kitchen floor, or your storefront, you don’t have to settle for basic gray anymore. Decorative concrete is here to stay in Twin Falls, and Orr Floor Care is ready to help you get ahead of the curve.
We’ll walk you through every option—polished concrete, flake epoxy, resurfacing, stains, overlays—and help you figure out what fits your space and your goals, not just what’s trendy. No pressure. No fluff. Just honest answers and high-quality work.
Call us today at (208) 404-6679 or shoot us an email at [email protected] and let’s talk about how we can make your floors the best feature in your home or business.
When you're ready, we'll bring the experience, the gear, and the grit to get it done right.